Maintenance strategies are important to mitigate the risks associated with system failure and deterioration. They entail a set of activities on the component level, such that each component can reach its expected service life. A large system like a school is comprised of many components, each requiring a set of unique maintenance activities. To reduce the systems downtime and to maximize the time intervals between maintenance activities, the associated activities can be bundled. The disjoint sets of activities can be optimized by maximizing the overlap of maintenance activities that can happen concurrently.
This section will introduce the maintenance activities that are required for each of the components in the 50-year lifespan of the school. It will then introduce two integrated maintenance strategies for components associated with the building envelope and interior, defining intervals and durations. Finally, the two distinct maintenance strategies will be combined and optimized by systemically exploring possible overlaps in maintenance activities, minimizing overall system downtime, and maximizing the gap between maintenance activities.
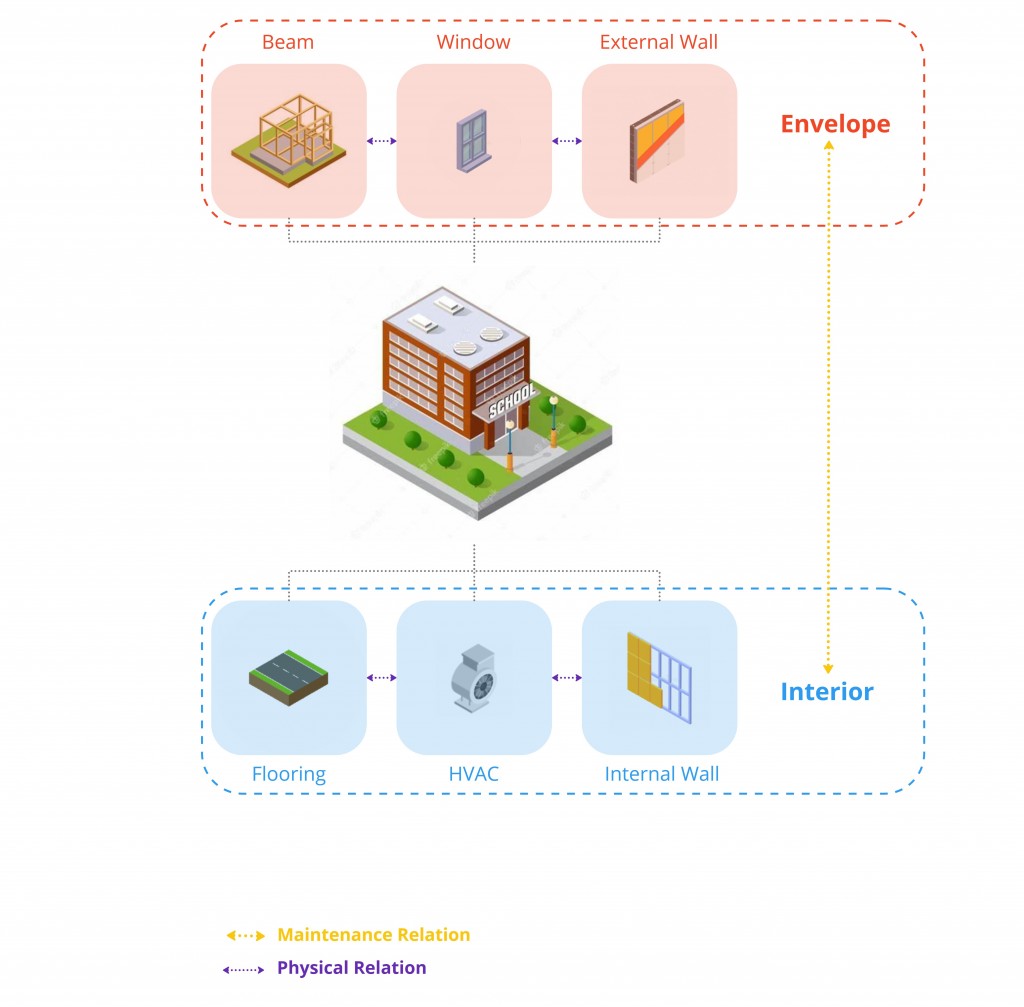
Individual Components
Each component requires a unique set of maintenance activities that have to be carried out at different frequencies and take a different amount of time to be completed. Maintenance activities cover a variety of aspects from visual inspections (i.e. glulam beam), routine maintenance (e.g. cleaning, sealing, crack repair of drywalls), to partial component replacement (e.g. exchanging window frames). Figure 2 lists the maintenance activities associated with the individual components.
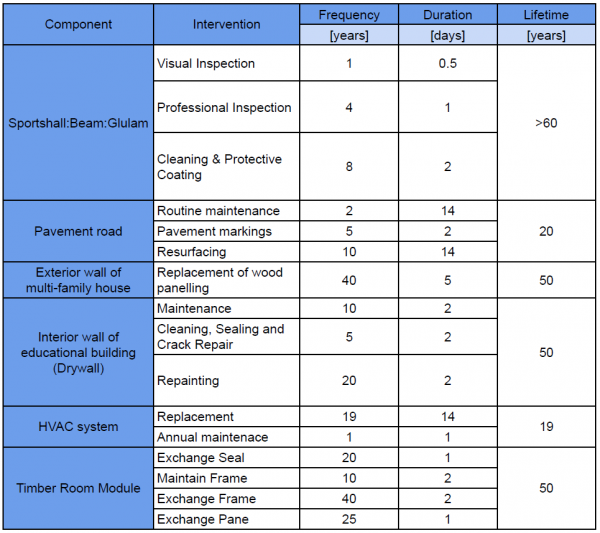
In order to evaluate these maintenance activities in a system context, three aspects have to be considered: their frequency, the duration and the expected service life associated with the components.
Regarding the expected service life, most components have an expected service life of 50 years or more, matching the service life of the school. However, the service life of the pavement road which is repurposed as poured asphalt flooring system and the HVAC system have a significantly shorter service life. Thus, any maintenance strategy for the school must take into account major overhauls of the flooring- and HVAC system at intervals determined by their individual service lifespan.
On the other hand maintenance frequency and duration are important metrics to consider when trying to optimize maintenance strategies. Reducing the frequency of maintenance activities, increases the time interval between interventions. While reducing the duration of interventions directly, reduces the systems downtime. The next section will consider these measures to bundle maintenance activities for the school’s interior and envelope components.
Maintenance Strategies for School Envelope and Interior
In this step we bundle the components and their maintenance activities into two groups: school envelope and interior. The underlying assumption here is that, since the members of the component groups share a physical connection, their associated maintenance activities need to be coordinated in more detail. Thus, we considered where they can be carried out concurrently and where they need to be conducted in sequence. Wherever maintenance activities can be bundled and maintenance work can happen concurrently, the system downtime can be reduced significantly.
Building Envelope
The combined maintenance strategy for the building envelope entails three sets of maintenance activities, including frequencies and durations (Figure 3-4). It entails all maintenance activities required for the components of the building envelope.
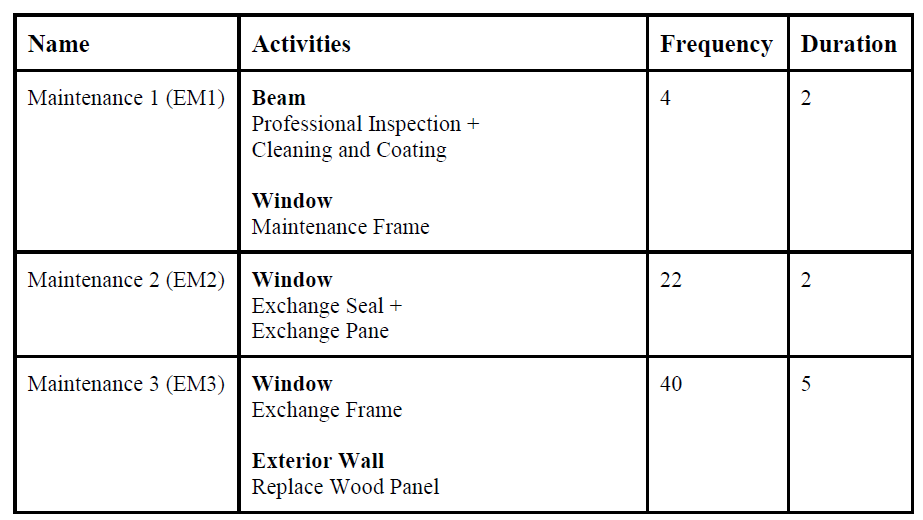
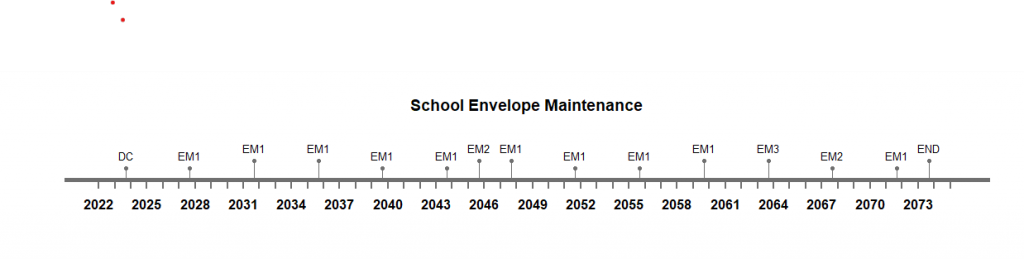
In the combined maintenance strategy for the building envelope, the visual inspection of the beams is omitted, since it is assumed that it can be carried out by the facility manager without causing downtime to the system. For EM1 the maintenance frequency for cleaning and coating of the beam, as well as maintenance of the window frame have been increased and bundled with the professional beam inspection. It is assumed that this increases the longevity of the components while reducing downtime, since these measures can be carried out concurrently. Maintenance activities associated with the window in EM2 must be carried out in sequence, resulting in a downtime of 2 days. On the other hand, the activities of EM3 can be carried out concurrently, causing a downtime of 5 days.
Building Interior
The combined maintenance strategy for the building interior again entails three sets of maintenance activities, gathering all required interventions for its components (Figure 5-6).
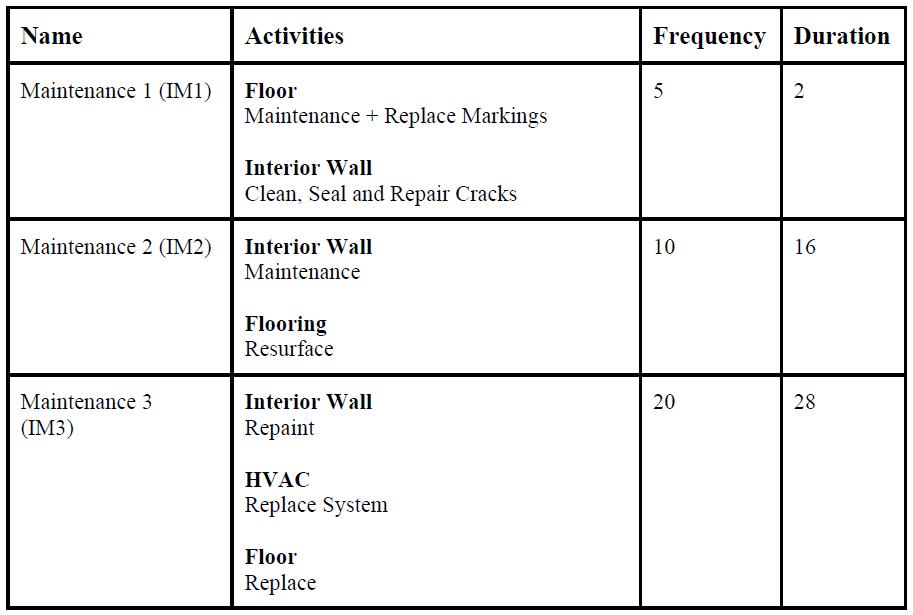

Routine maintenance of the flooring system and HVAC are omitted, assuming that they can be carried out by the facility manager or other trained personnel without producing any downtime in the system. Activities associated with IM1 can be carried out concurrently, resulting in a downtime of 2 days. In IM2 the interventions must be carried out in sequence resulting in a downtime of 16 days. Lastly, in IM3 the interior components require a major overhaul, the flooring system and HVAC system need to be replaced and the interior drywalls need to be repainted. These activities can only partially be carried out in concurrence resulting in an overall downtime of 28 days.
Combined Maintenance Strategy
In the next step the maintenance strategies for components of the school envelope and interior are combined. The aim is to indicate the overall system downtime and frequency of interventions. In this context it is assumed that all activities of the two distinct strategies can be carried out concurrently.

As can be seen from Figure 7 the combined downtime due to maintenance interventions is 120 days. Furthermore, due to the lack of coordination between the maintenance strategies for building envelope and interior, distinct intervention events happen much more frequently than might be necessary, producing more system downtime.
To explore the design space for more efficient combinations the static assumption on the frequency of the maintenance intervals is loosened according (Figure 8).

In this context it is assumed that the associated maintenance activities can be carried out at any point in time over a 5-year interval. Based on a set of preferences and defined ranges, a simulation checks all possible combinations of the two maintenance strategies, to find the most efficient solution. As previously mentioned, the preferences here are: to minimize system downtime over the entire lifecycle of the structure, while on the other hand maximizing the distance between maintenance activities.
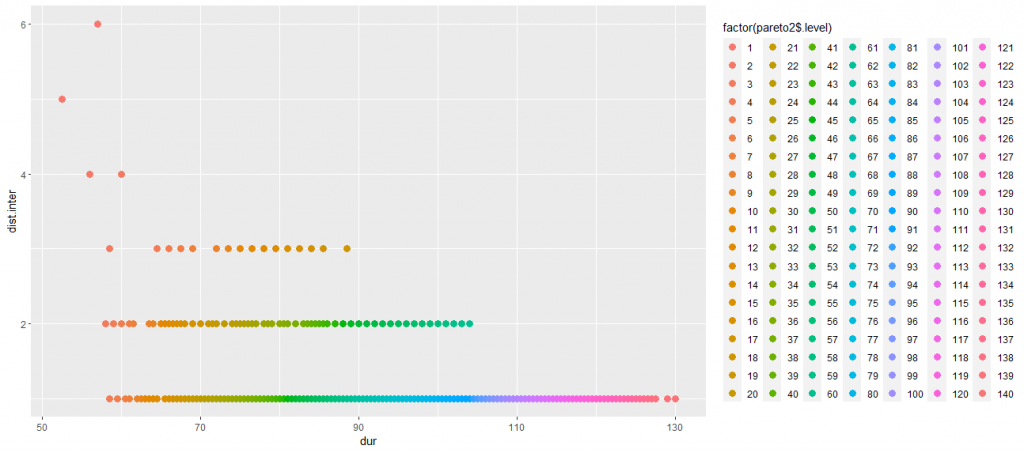
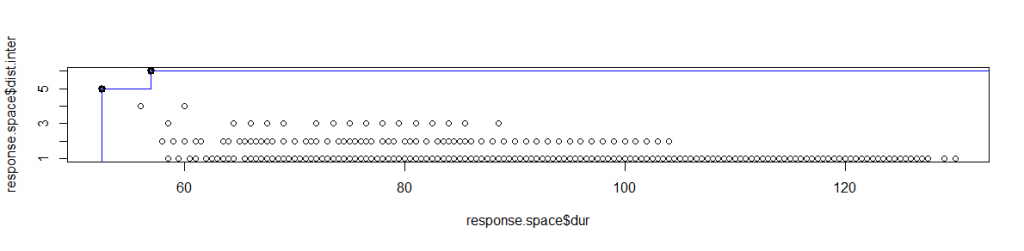
For the evaluation of the combinations three distinct preferences have been defined. The first preference is to minimize the system downtime due to maintenance interventions. The second preference is to maximize the time between consecutive interventions, while the third is a combination of both. Figure 9. shows all possible combinations of maintenance strategies, ranked based on their performance regarding the third preference. As can be seen from Figure 9-10. there are two preferred options minimizing downtime and maximizing the time between interventions.
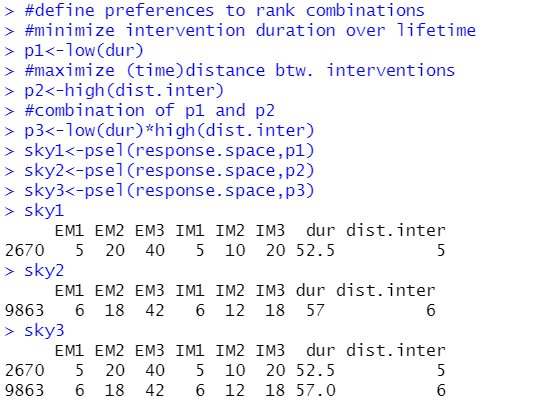
While both options perform well for preferences 1 and 2, the first option (2670) minimizes the duration of interventions over the lifetime of the school to 52.5 days, requiring interventions in 5-year intervals. On the other hand, the second option maximizes the time between interventions (6-years), resulting in an overall downtime of 57.0 days.
In the context of a school building, we chose the first option as the best combined maintenance strategy. The assumptions here are that considering overall downtime is very important in the school context to minimize interruptions. Furthermore, it is assumed that frequent maintenance activities and inspections increase the longevity of the components.
Introduction | Integration Context | Maintenance Strategies | Life Cycle Analysis | Multi Objective Optimization