Design Challenge
The design of an offshore wind turbine requires the consideration of various parameters that have a direct influence on the performance and efficiency of the turbine. These parameters include the depth and diameter of the foundation piles, the size of the foundation plate, the diameter of the tower and its material thickness, the dimensions of the nacelle and the diameter of the rotor blades. In this task, a parametric model for an offshore wind turbine is developed, and different design alternatives are analyzed based on these variable parameters.
Design parameters and criteria for high-performance
The selection of design parameters for the offshore wind turbine and the criteria for high performance are carefully defined to meet the specific requirements of the turbine. The High-Performance Parameters (HPC) can define the overall Wind turbine design, and therefore they are an important tool for decision-making processes.
HPC: Power generation
Power generation is a decisive factor in the performance of an offshore wind turbine. By optimizing design parameters such as tower diameter, rotor blade diameter and nacelle size, the aim is to achieve maximum energy generation from the turbine. Efficient energy production not only contributes to the profitability of the turbine but also to the reduction of CO2 emissions and the promotion of sustainable energy production.
HPC: Material consumption
Material consumption plays an essential role in the economic and environmental assessment of an offshore wind turbine. By optimizing design parameters such as foundation piles, tower diameter and material thickness, we aim to minimize material consumption without compromising the structural integrity and reliability of the turbine. Reducing material consumption not only contributes to the cost efficiency of the turbine but also to reducing the environmental footprint and conserving natural resources.
HPC: Material costs
Material costs are a major component of the total cost of an offshore wind turbine. By selecting cost-efficient materials and optimizing design parameters, the aim is to minimize the material costs of the turbine without compromising quality and performance. Effective control of material costs contributes to the competitiveness of the turbine in the renewable energy market and enables a profitable investment in clean energy.
HPC: Environmental Impact
The environmental impact is a significant consideration in the design and operation of offshore wind turbines. By optimizing parameters such as rotor blade length, superstructure nacelle dimension, substructure tower radius, height, wall thickness, foundation pile depth, and radius, we aim to minimize the environmental impact of the turbine. This includes reducing noise pollution, mitigating visual impact, and minimizing disturbance to marine ecosystems. By carefully considering these factors, we can ensure that offshore wind turbines contribute to sustainable energy production while minimizing their carbon footprint.
Design Parameters
In Figure 1 the essential design parameters for the development of the offshore wind turbine model are presented. Each parameter is carefully defined, and the range between their minimal and maximal values, along with various combinations, forms the design space within which the turbine is optimized for optimal functionality and reliability.
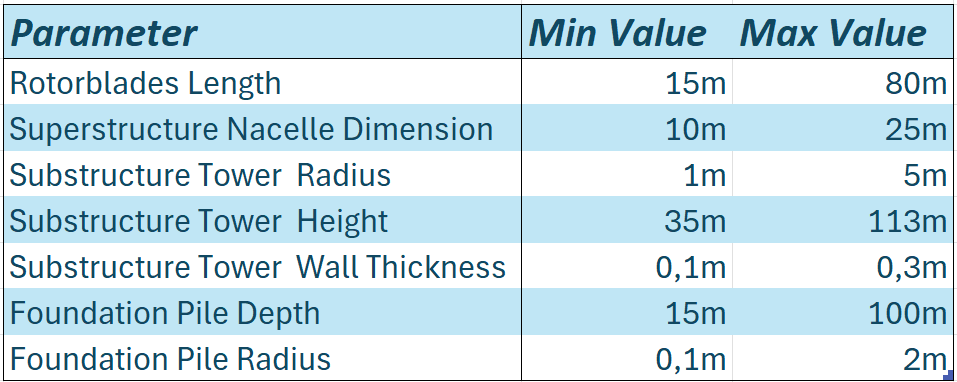
Parametric Model Description
The Dynamo script for the parametric generation of the model is shown in Figure 2. The model can be divided into areas A, B, C and D. The structure of the offshore wind turbine design is based on the structure shown in Figure 3 of the previous chapter. Area A shows the previously mentioned design parameters. Area B represents the superstructure, with the scripts for the rotor (purple) and the nacelle (orange) defined. Below this, in C, are the scripts for the substructure, which includes the tower (green) and the foundation (blue). Area D, the HPC, could not be completed before the editorial deadline.
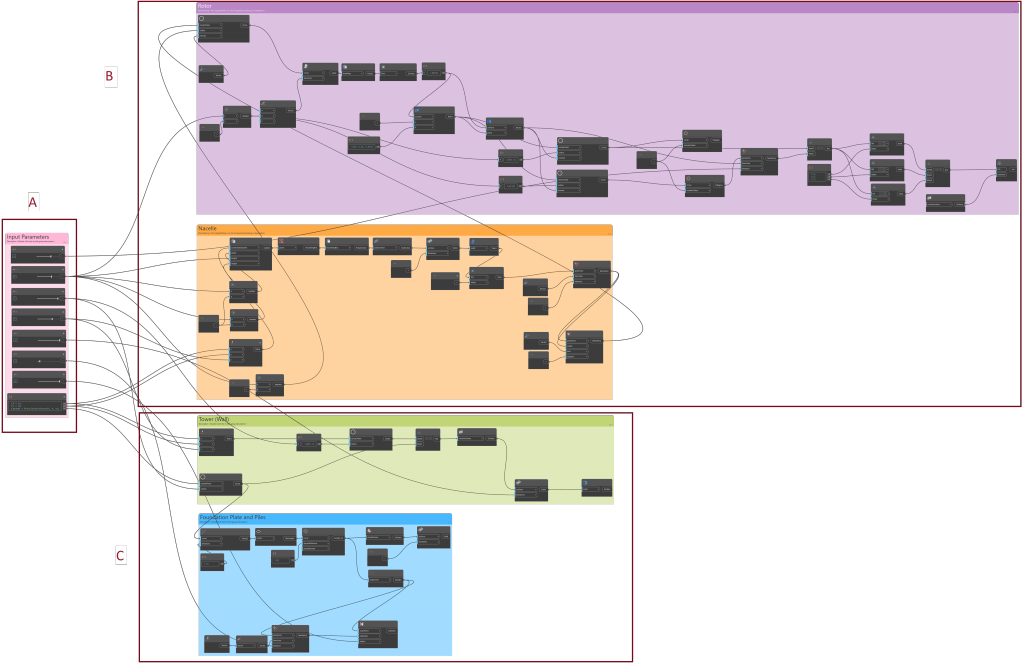
Engineering challenges
The design and construction of an offshore wind turbine present several engineering challenges. It includes installing the foundation structures in difficult offshore conditions, optimizing the tower and nacelle design for maximum performance, economic and material efficiency and environmental impact of the turbine.
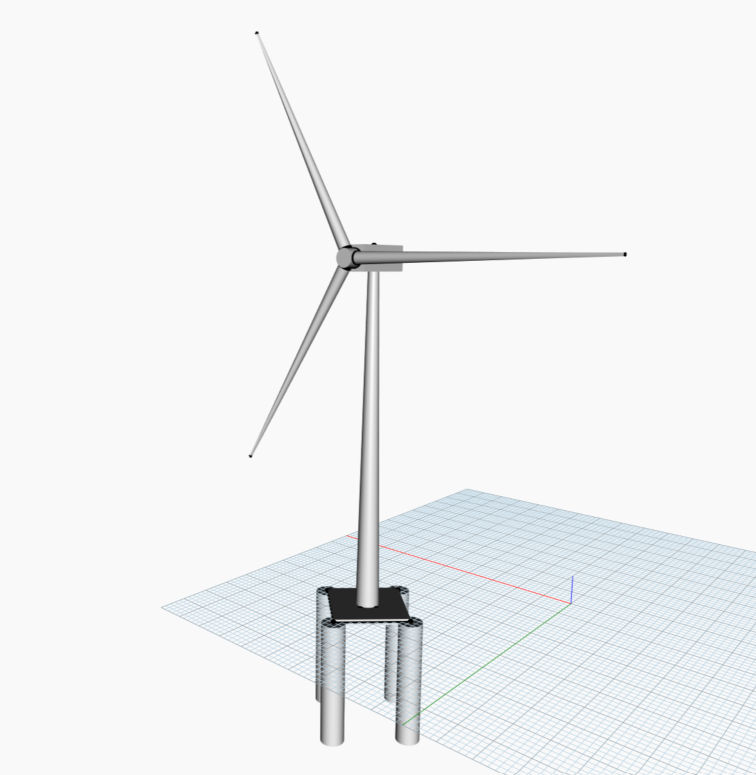
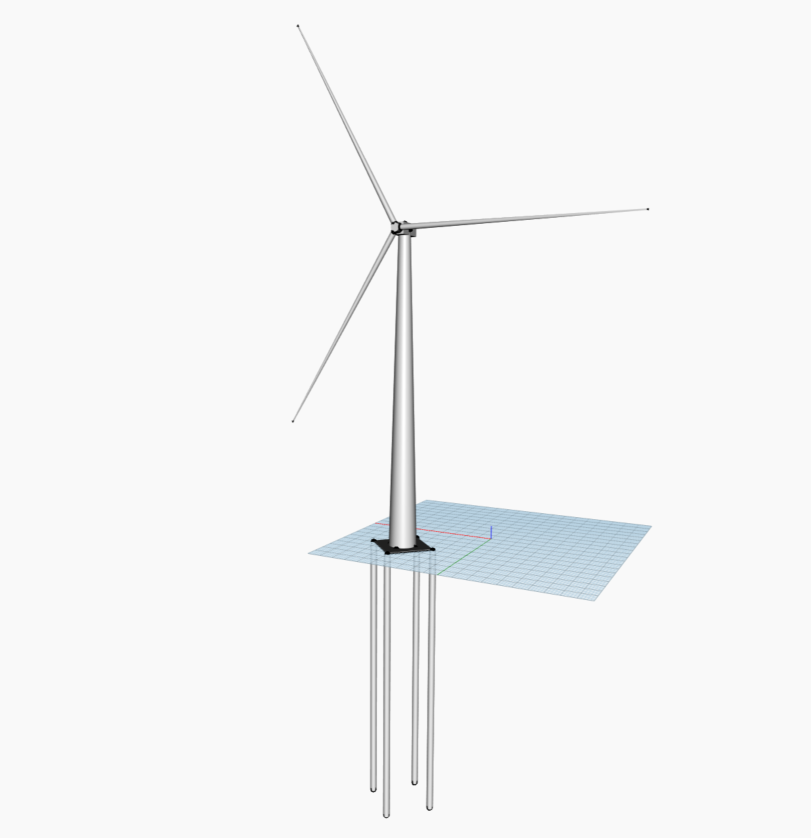
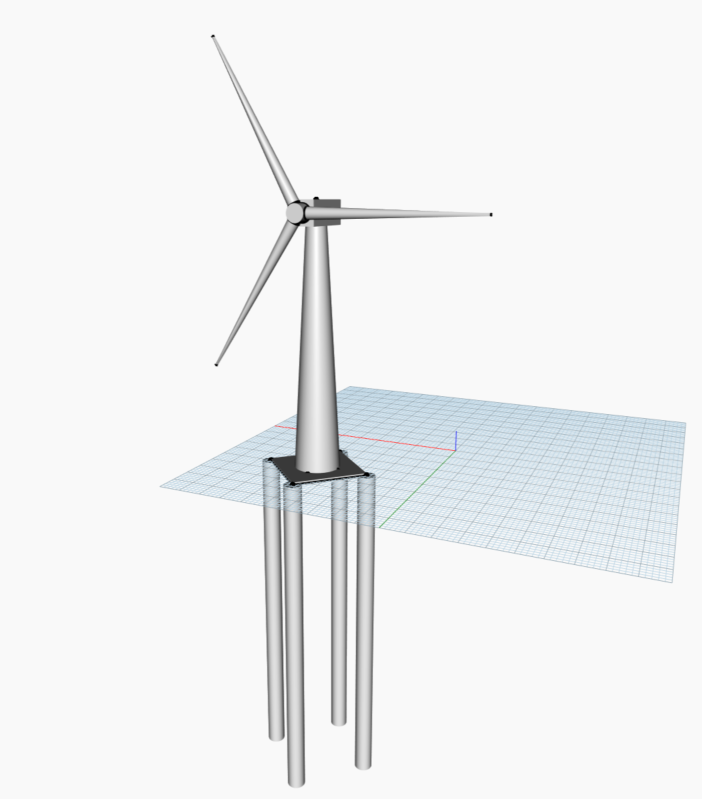
By adjusting the design parameters, different design alternatives can be developed for the offshore wind turbine, including different combinations of foundation piles, tower diameters, material thicknesses, nacelle sizes and rotor blade diameters. These design alternatives will be evaluated based on their impact on the turbine performance criteria to determine the optimal configuration. Nevertheless, it should be emphasized that the model offers limited possibilities. For example, the tower height in the model does not influence the cross-section parameter, which should be related. Another problem is that there is no connection between the tower height and the rotor diameter. These cross-section parameters should be linked in a more complex version of the model to make the design more realistic. These inconsistencies can be accepted when creating a conceptual design for this model, as the tower design will be further developed in later stages of the project.
Parametric Model
← Ontology | Back to Individual Systems